A common challenge for manufacturers is discerning the actual costs necessary to produce finished goods. The importance of identifying the true cost of produced goods cannot be understated. Manufacturing companies that are able to accurately account for inventory costs will be in a better position to analyze gross profit. Gross profit analysis is designed to identify the reasons why the gross profit margin changes from time to time, so that management is able to take action and bring the gross margin in line with expectations. Obviously, a decline in gross profits could indicate a serious problem either in sales, materials, labor, or overhead, and so the impact of this figure is highly depended upon. Accounting for all manufacturing costs in your inventory is very effectual on your business.
There are two primary cost groups – direct and indirect costs – that come into play.
Direct Costs – specifically related to the production or procurement of the item, be it the cost from the vendor or the cost of labor to produce the item.
Indirect Costs – used by multiple activities and are needed to run the company. Some common examples are electricity, rent and administrative expenses.
Direct costs are generally easier to determine. The cost of a material from a vendor is a known value, and while that might change from purchase order to invoice, this can be easily identified. Inbound materials can have other costs associated with the receipt such as freight, taxes or tariffs. These costs,-– commonly referred to as landed costs, –are directly attributable to the item and should be included in the valuation of that item.
This is the true cost to bring that product in from the vendor.
For example, let’s suppose a manufacturer creates a purchase order for 5,000 pounds of vanilla bean oil with its vendor, who upon shipment issues an invoice for $6,500 ($1.30/pound).
In addition to the vendor invoice, there is a $500 freight charge from a third party carrier, as well as a $200 customs charge since this was purchased outside the country.
The shipment is handled by a third party trucking company, resulting in a $500 invoice.
A common practice among many manufacturers is to process the initial invoice amount from the vendor for $6,500 in order to correctly balance the amount due to the vendor. In this scenario it would now show the cost of the vanilla bean oil at $1.30/pound. The freight invoice and customs charge ($700) would be processed and entered into an expense account in the general ledger. That expense is incurred at that time versus attributing those costs to that of the raw material, which once consumed and sold, would be reflected in the cost of sales.
Capturing landed costs is a reliable way to achieve a true depiction of the value of the inventory. The benefit of capitalizing these additional costs becomes apparent once these items are consumed and the costs are rolled into finished goods. By identifying the actual cost of material that goes in to a finished good, the sales team can more accurately price out finished products and analyze sales data and profitability.
There are other cost types that can be accounted for by manufacturers as well. Labor is typically a direct cost that can be easily applied to the production of a finished good. By tracking the number of hours and employees working on a production ticket, the cost of labor can easily be identified and included in the cost of the final product. For some companies, however, it may not be easy to track a specific laborer, exact time spent and hourly wages for a ‘per production order’ basis, but it is possible to determine a standard rate of which to apply.
Using the earlier example of the vanilla bean oil purchase, we will now evaluate the manufacture of personal care products using the vanilla bean oil infused into its shampoo. The cost to manufacture the shampoo is $67.00 per 50 pound drum.
In order to meet a customer order of 200 drums, the following components are needed along with the purchase price from the vendor:
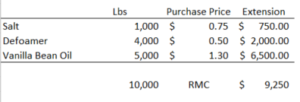
Also needed, are 200 drums which were purchased at $5.00 per each.

In looking at just the purchase price, the cost of materials and packaging to produce 200 drums of the shampoo is $10,250, or $51.25 per drum. At a sales price of $67.00 the manufacturer – equates its profit to be $15.75 and a profit percent of 23.51%.
However, once the landed costs of the vanilla bean oil are included, along with capitalizing the labor and overhead costs associated with the production of this product, a completely different story can be told.
The difference is rather significant. Rather than the vanilla bean oil costing out at $1.30 per pound, that cost rises to $1.44 per pound following the additions of the freight ($500) and custom ($200) charges in the cost.
In addition, this company has set a standard labor rate of $.05 per pound produced for mix labor, $1.25 per drum as the standard rate for filling labor, and uses a rate of 10% of labor as their overhead absorption factor.
Once these costs are included, the cost to produce the 200 drums has a much different outlook.
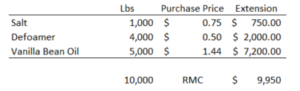


Now that all applicable costs are accounted for, the profit percentage decreases from 23.51% down to 12.5% – a significant difference in realization.
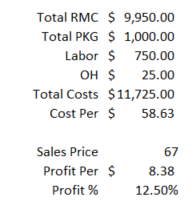
By including the landed cost to the raw material and capitalizing labor and overhead into the production process, companies are able to see a more complete picture into the profitability from sales and are equipped to make better decisions regarding sales pricing.
An effective inventory cost management system allows manufacturers to process true costs, real margins, and operational consistencies in order to continuously monitor and assess overhead, labor and production value.
For more information on inventory cost management and accountability for your M&D needs, please contact a Sikich advisor.