I was recently consulting for a large distribution center and discovered some Receiving to warehouse putaway processes that could be encountered at other distribution-based centers and large manufacturing customers with rapid and diverse receiving docks. I realized some of these activities can be accomplished with Receiving, putaway, reservation management and the Advanced Warehousing Dynamics 365 mobile app.
Sitting on the Dock of the Bay, I noticed that the customer had a straightforward process where the warehouse workers received items at the Receiving Dock, placed them in a bin and kept paper copies of what was received. There was a magic rock present to keep the papers from flying away and they didn’t seem to have many issues with missing Purchase Orders or paperwork. They received mixed pallets of items, shrink wrapped boxes, and even full pallets of material; there was no standard to how it was packaged or how it was delivered to the receiving dock. They did not have any food items or hazardous items, so Quality Control was not a problematic consideration. The dock was often cluttered, and tribal knowledge drove a lot of their process, but it was spacious and organized enough to keep things moving.
Microsoft Dynamics and Item Arrival Journals
The company was live on Microsoft Dynamics and has been posting Item Arrival Journals for years to get inventory into the ERP system. Up until this point, the product is physically in the building, but it is not actually in inventory in Microsoft Dynamics until the Journal is posted. The Item Arrival journal posts with the item number, quantity, PO Number, etc.… to a receiving dock location. They had some code customizations that blocked sales order reservation when items were at the receiving dock. The workers took advantage of their tribal knowledge and some Sharpies to know which items needed to be moved into inventory. Most of the time, they were a day behind, and they knew what they received yesterday was probably ready to be moved today. One interesting piece was they used a custom WMS solution on the dock. They would scan what they remember taking off a truck yesterday and if it came up with the receiving dock location on the gun, it meant the journal had been posted. If the location was blank, the Item Arrival journal has not been posted yet.
Where do I put my stuff?
Many Dynamics Consultants are familiar with the term directed putaway and it was a big addition for Dynamics WMS when it was included in the product. Directed putaway is when the system tells a worker where to place an item in the warehouse. It follows numerous rules and logic to find and use the most desired putaway location. Directed putaway requires a lot of discipline in the warehouse, there needs to be space for things to go, and extremely accurate inventory. None of these key items were evident during discovery, so we decided to use a Suggested Putaway approach. The customer’s homegrown WMS solution had something similar in the solution. A putaway worker would scan an item’s barcode to find out if was at the dock. If it had a receiving dock location, they could start the warehouse putaway process. They would then use a search function on the scan gun to look for locations in the warehouse that contained this item. Like item was very common for this distribution client. With like item being so common, putaway workers were required to consolidate whenever necessary. The search function was key for them to be able to determine like item locations, perform consolidation work and place new inventory away. If no location was found containing a like item, then an empty rack location was chosen. Although a lot of the suggest putaway and reservation process was customized for this client in their homegrown WMS solution, I was able to reproduce a better solution leveraging Dynamics 365 advanced warehousing principles as well as setting up proper configurations for the mobile device.
To summarize to this point:
- Receive Pallets/Boxes of items
- Place PO/Receipts list into bin
- Receiving Clerk periodically picks up the paperwork
- Receiving Clerk posts Item Arrival Journals for the purchase orders received
- Putaway workers scan items at the receiving dock for movement
- Workers consolidate and place over flow on top shelf of rack
- If no like item location is found, worker selects an empty location for putaway.
- Items are now available for sales order reservations
Setting up the Mobile Device Menu Item in Dynamics 365
As some of you may know, license plate tracking is required for advanced warehousing processes. I configure a menu item on the scan gun to generate a license plate during the pick and put process for receiving putaway. The key setup is Mode = Work, Generate License plate = Yes, Work creation process is Warehouse transfer. I will review the Default Data highlight, Display inventory status, and Use default data later in the article.

Dinner party for 2 please…
Default Data is used so I could manage reservations. I configured a RECV Warehouse where all Item Arrival Journals would post receipt of inventory. All customer’s and vendors were set to a different default warehouse so reservations would never be placed against inventory in the RECV warehouse. This basically gives the company a place to receive product and putaway before sales orders can be placed against it. They could do adjustments, inspections, etc., and not have to worry about sales order reservation.
Once the inventory was in available status in the correct warehouse, sales orders would reserve the quantity. Additionally, a user must use the auto sales reserve process to update the on-hand quantity if the sales order was put in the system before there was actual inventory.

Once this batch process is run, the sales order will automatically be released and be available to be placed on a wave. Since our customer was doing wave picking this was quite handy.
Location directives are the center of the whole operation (below). The first is a simple pick from the warehouse RECV dock.
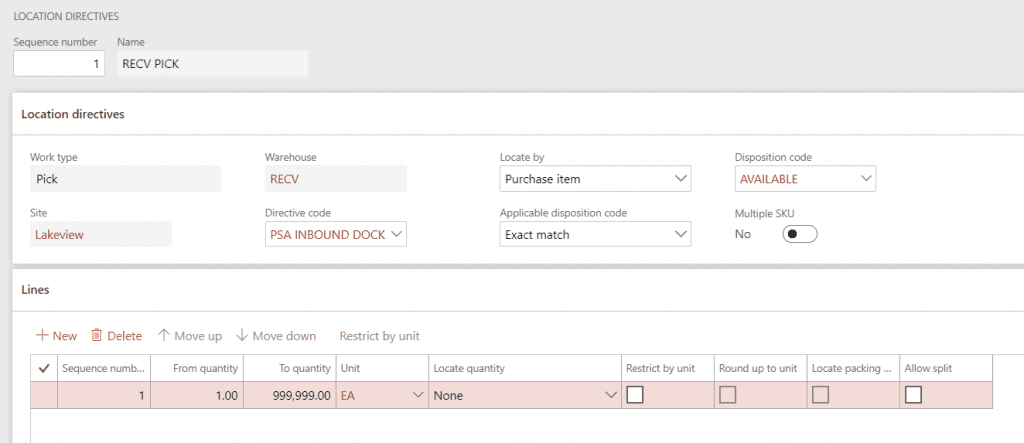
Action queries are helpful in narrowing your pick locations in the RECV warehouse. (shown below)
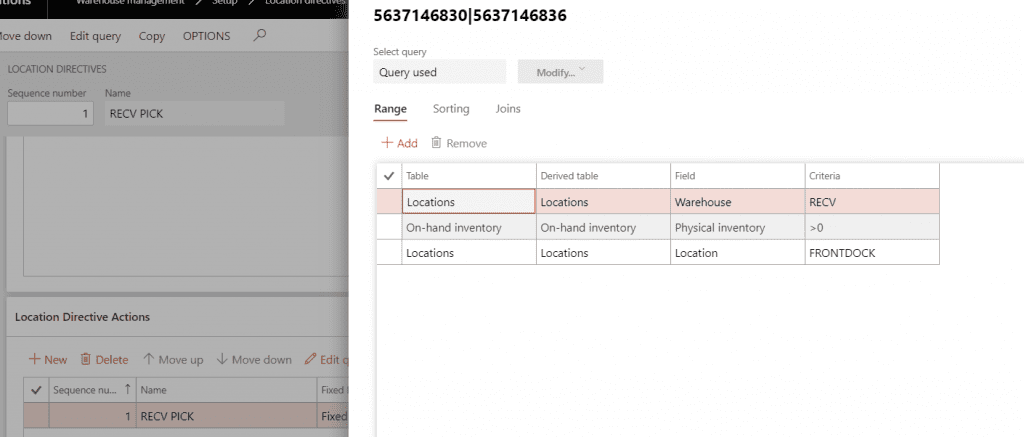
I created a sequence for this Named Suggest Like Location. This sequence will find like item locations and consolidate first, if no like item locations are found, the second action looks for an empty location in the warehouse. If allow split is selected, this will allow the worker to putaway (move) items to a location, consolidate to that location and then split the remaining QTY to an overflow rack location. If all the product will fit in the suggested location by doing consolidation and placing a few extras on top of an empty pallet, this is probably the most desired outcome. Be sure to include the inventory unit, especially if you have unit conversions.
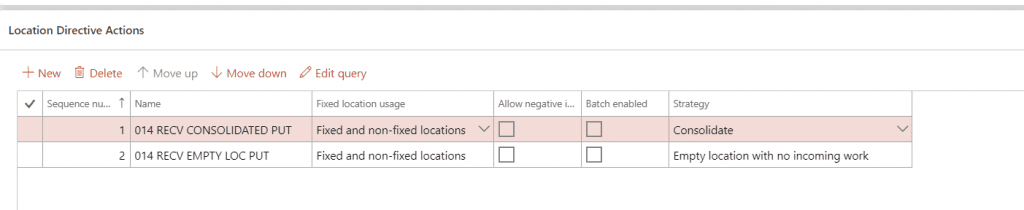
Worker Setup
Allowing Pick and Put location override is a good idea to have enabled, which allows WMS putaway workers to edit the locations being shown on the scan gun. The other key piece is allowing movement of inventory with associated work should be enabled, since this is exactly what the worker is doing.
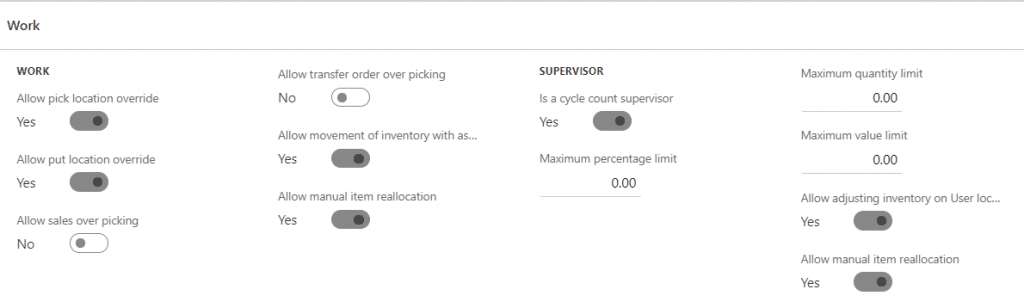
Now let’s start picking from the dock
This is the first screen in the warehouse putaway process a user will see on their handheld device. They should scan the location in which they are moving received product from. Next, scan the item. If it is the only pallet or box of inventory on the dock with a matching item number, the quantity will be displayed for you. Note: The client also did not print item labels. We were able to accomplish this by scanning item UPC barcodes.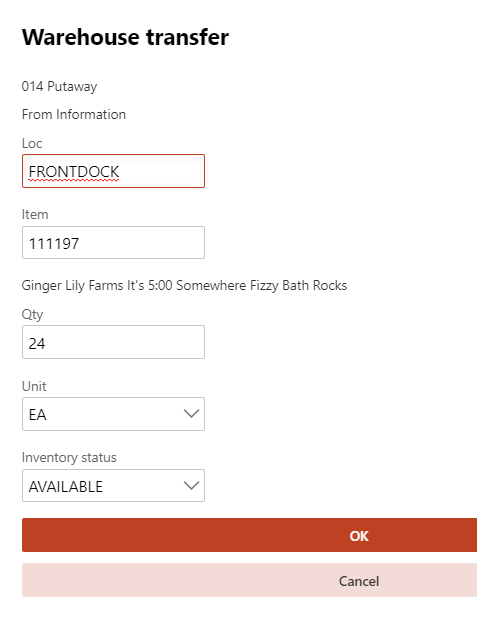
This screen shows the suggested location in the warehouse which contains a like item. This is the suggested putaway piece. Users ideally want to place inventory where it exists to perform consolidation.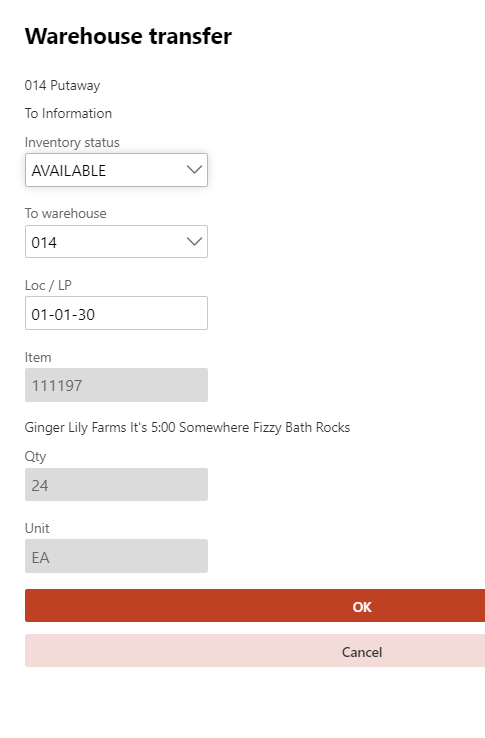
If split putaway is enabled, a user should be able to split the putaway. Ideally, we will be able to putaway the quantity of inventory that will fit into the suggested location and place the remaining inventory in a secondary overflow rack. This is where the split put is necessary.
And we should arrive at the famous “Work Completed” screen which completes this process.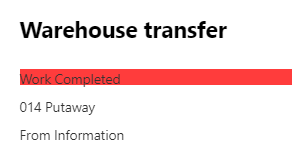
Have any questions about optimizing your warehouse putaway or Dynamics 365? Please contact us at any time!